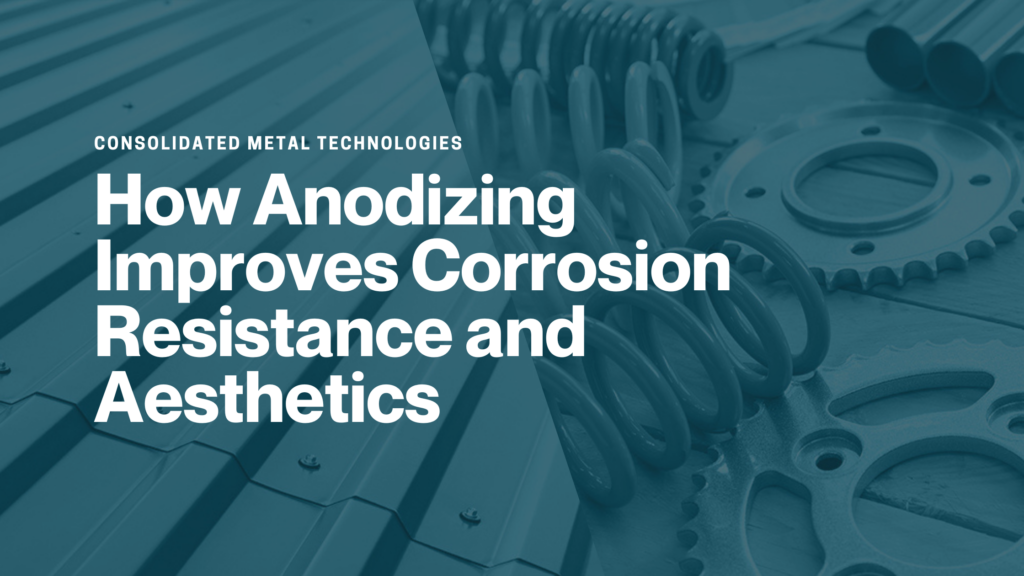
In the world of metal finishing, anodizing stands out as a highly effective method for enhancing both the durability and appearance of metals. Whether for industrial applications or consumer products, the anodizing process significantly improves corrosion resistance while offering a sleek, attractive finish. But how does anodizing work, and why is it a preferred choice for protecting metals?
Understanding the Process
Anodizing is an electrolytic passivation process that strengthens the natural oxide layer on aluminum surfaces. During the process, the metal is submerged in an electrolyte solution, and an electric current is applied. This controlled oxidation reaction thickens the surface oxide layer, making it more resistant to environmental factors such as moisture, chemicals, and extreme temperatures. Unlike coatings or paints that sit on the surface, anodized layers integrate with the metal, providing superior adhesion and long-lasting protection.
Learn more about Passivation in our blog
Corrosion Resistance: The Benefits
One of the primary benefits of anodizing is its exceptional anodizing corrosion resistance. The anodic layer forms a robust barrier that shields aluminum from environmental factors, dramatically enhancing its corrosion resistance. This makes anodized metals ideal for applications exposed to harsh conditions, including marine environments, aerospace components, and architectural structures. Because the anodized layer is non-conductive and does not peel or chip like traditional coatings, it ensures extended performance and reduced maintenance costs.
Additionally, it enhances wear resistance by creating a hardened surface that minimizes wear and tear, significantly extending the lifespan of aluminum components.
Enhancing Aesthetics
Beyond durability, anodizing also enhances the visual appeal of metals. The process allows for a variety of finishes, including matte, glossy, and textured surfaces. Thick, porous coatings can absorb dyes, producing vibrant colors, while thin transparent coatings create light interference effects, resulting in a distinctive and unique appearance. The uniform and smooth appearance achieved through anodizing makes it a preferred choice for consumer electronics, automotive trim, and decorative architectural elements.
Standards and Capabilities at CMT
At CMT, our process meets stringent industry standards to ensure the highest quality:
- MIL-A-8625 Type II, Class 1 & 2: complies with military specifications for anodic coatings, ensuring superior durability and protection.
- ASTM B580: adheres to the American Society for Testing and Materials standards for anodizing, ensuring consistent and reliable results.
We offer Type II anodizing (Sulfuric Acid) with a wide range of options to meet your specific needs:
- Standard colors: clear, black, blue, gold, purple, red, green.
- Custom colors: available on request to match your exact specifications.
- Tank size: our largest tank measures 44 in. x 46 in. x 72 in., allowing us to handle both small and large components efficiently.
Choose CMT for High-Quality Anodizing Services
If you’re looking for superior anodizing corrosion resistance and enhanced aesthetics for your metal components, Consolidated Metal Technologies (CMT) has the expertise and technology to deliver high-quality results. Our precision anodizing process ensures that your materials are not only durable but also visually appealing.
With industry-leading quality assurance, advanced facilities, and extensive customization options, CMT is your trusted partner for anodizing solutions. Contact CMT today to learn more about our services and how we can help protect and enhance your metal components.
Request a quote now and experience the benefits of anodizing for your next project!